Jeune pousse issue en 2015 d’un projet de recherche de l’Ecole d’architecture de Paris Malaquais, XtreeE a mis au point des systèmes d’impression 3D à grande échelle d’éléments de structure pour la construction qui séduisent de plus en plus architectes, designers et de préfabriquants dans le monde entier. Pour répondre à la demande tout en s’inscrivant dans un développement durable, elle change de stratégie et de braquet pour constituer d’ici à 2025 un réseau mondial de 50 unités d’impression connectées, qui produiront localement.
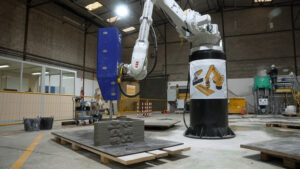
Quand on est un non-spécialiste, pour visualiser ce que signifie concrètement l’impression 3D à grande échelle de pièces en béton ou en ciment réalisée par une machine d’XtreeE, rien de mieux que de visionner des photos (ci-contre, chez Spie Batignolles), voire une des vidéos disponibles sur le site de cette startup – plus précisément une « scale-up » – issue d’un projet de recherche au sein de l’Ecole d’architecture de Paris Malaquais.
En voici une qui montre la réalisation d’un prototype de récif artificiel en forme de dôme filaire pour Seaboost, spécialiste de la protection de la biodiversité marine. Vissée au bout d’un énorme bras robotique du genre de ceux qu’utilisent les usines automobiles, la tête d’impression bi-composant bourrée de technologies coule avec une précision au millimètre des fines couches de béton en suivant le tracé entrelacé de la structure, pivotant jusqu’à à 90 °. En 35 minutes, le prototype aux dimensions honorables (1x1x1 m), qui a nécessité 35 litres de matière, est terminé.
« Ce que nous apportons à la construction, c’est l’automatisation et la digitalisation », précise Dominique Corvez, qui a pris le 18 juillet dernier la direction de cette jeune pousse d’une vingtaine de personnes – essentiellement des ingénieurs- en tant que président-directeur général. « Nous, nous proposons de couler au plus juste ».
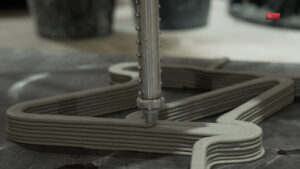
Mais XtreeE ne vise pas le marché des pièces de structure standards, comme les parpaings, dont la production est déjà largement automatisée. Ses systèmes d’impression 3D sont particulièrement pertinents « pour des pièces nécessitant des moules », typiquement les finitions de façades. Ils permettent aussi de tester de nouveaux mélanges de matériaux innovants, d’optimiser la fabrication des pièces, et de réduire, au final, l’empreinte carbone des constructions. Cerise sur le gâteau : le système, et en particulier la tête d’impression d’une cinquantaine de kilos, s’adapte à divers modèles de bras robotiques, comme ceux de Kuka ou ABB.
Avec les contraintes environnementales qui se durcissent et une industrie de la construction toujours en quête de performance et de gain de productivité, le champ qui s’ouvre à XtreeE est immense : sa technologie, couverte par une dizaine de brevets internationaux, intéresse architectes, designers, ingénieur de la construction dans le monde entier.
De la production à la demande à la vente de système clés en main
Créée en 2015 par les deux architectes ingénieurs Alban Mallet et Romain Duballet, et longtemps hébergée au sein du laboratoire PIMM de l’école des Arts et métiers avant de s’installer dans ses propres locaux à Rungis, elle a d’ailleurs bénéficié au départ du soutien de Vinci et Holcim (ex. Lafarge), qui ont pris des participations au capital, mais aussi du fonds dubaïote Shibumi International, qui met des tickets dans des startup innovantes du secteur de la construction. Il a fallu trois ans pour développer ses technologies puis commencer à les commercialiser. Avant de faire évoluer son modèle.
Au départ, les fondateurs pensaient développer en France, à l’échelle industrielle, leur activité d’impression 3 D de pièces et éléments préfabriqués à la demande. Mais c’est sur des unités d’impression clés en mains que la demande s’est portée. D’autant plus qu’avec la crise Covid, les problèmes de transport et les exigences de décarbonation de l’industrie de la construction ont bouleversé les besoins et les pratiques du secteur, accélérant la transformation vers des modèles plus responsables. Il a fallu faire évoluer le modèle.
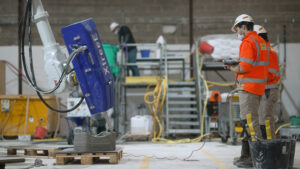
Aujourd’hui, y compris à l’export, XtreeE vend des systèmes complets connectés et des services d’accompagnement, pour favoriser la conception locale et l’utilisation de matériaux locaux. « On transporte juste la tête d’impression » souligne Dominique Corvez, qui a justement été recruté pour prendre en main l’accélération de ce déploiement international.
Concrètement, une unité d’impression XtreeE type est composée d’un bras robotique que l’on trouve sur le marché, équipé d’une tête d’impression bi-composant XtreeE, d’une unité de préparation des mélanges de matériaux qui alimentent la tête d’impression, et d’un poste de contrôle. Le tout doté des suites logicielles de la startup française, et pilotable à distance. L’ergonomie des interfaces a été soignée pour en simplifier l’usage : « un maçon peut faire fonctionner notre système », souligne le P-dg.
Outre le « hardware » et le « software », la jeune pousse propose également à ces clients, moyennant une redevance, tout un service d’accompagnement « pour les aider à concevoir et créer des projets d’objets ou d’éléments de construction en 3D » précise le P-dg. Il est proposé depuis sa plateforme en ligne dédiée « Printing as a service », qui contient tout un catalogue de produits certifiés et des outils numériques d’assistance à la conception et la réalisation.
Changer de braquet pour répondre à la demande
Sans effort de promotion ou de marketing, en bénéficiant de la notoriété acquise dans le secteur au niveau mondial grâce à son avance technologique et les publications des doctorants qu’elle a hébergés, XtreeE a déjà vendu douze sites d’impression 3D, en France et à l’étranger (Canada, Chine, États-Unis, Japon, Émirats arabes unis, Suisse). Ses clients – Dominique Corvez préfère parler de « partenaires » -, sont des centres de recherche universitaires, des entreprises générales du bâtiment, des préfabriquants.
En France, Spie Batignolles a déjà investi dans trois unités d’impression, aux Émirats arabes unis, c’est Vinci qui a donné le coup de pouce. Au Japon, durant la Covid, XtreeE a installé deux unités d’impression à distance en passant par un intermédiaire distributeur…
Les marques d’intérêt affluent. La recherche, en pleine ébullition avec les urgences climatiques, alimente la dynamique. « Nous avons énormément de demandes de la part de laboratoires universitaires qui travaillent sur les matériaux », se félicite Dominique Corvez.
Aux États-Unis, où les systèmes de la jeune pousse ont reçu la certification du NIST (National Institute of Standards and technology), un vrai sésame pour le marché nord-américain, une unité a été acquise par l’université Cornell, dans l’État de New-York, et une autre par l’université du Texas. XtreeE vient par ailleurs d’installer une nouvelle unité au Canada.
En France, où l’université de Toulouse vient d’acquérir un système, les visites sur le site de Rungis de clients potentiels se succèdent. Aux États-Unis, XtreeE fait visiter aux prospects les unités installées dans les laboratoires universitaires. Mais la jeune pousse, dont le chiffre d’affaires a été de l’ordre d’un million d’euros l’an dernier, peine à satisfaire ces demandes qui affluent. Il était temps de changer de braquet et d’accélérer son développement.
Changement d’organisation de la gouvernance et levée de fonds
La nouvelle stratégie est résolument mondiale. XtreeE vise à présent à déployer un réseau de 50 unités d’impression 3D dans le monde d’ici 2025. « Nous voulons monter en puissance dans la production de nos systèmes, et nous déployer en Europe et en Amérique du Nord », précise Dominique Corvez. Ce qui passe par un renforcement de son organisation, de ses moyens financiers et de ses ressources humaines, et notamment la constitution d’une équipe commerciale dont elle était dépourvue jusqu’à présent. « Nous voulons nous doter de bureaux régionaux dotés de showrooms et de démonstrateurs » complète le dirigeant.
L’arrivée d’un nouveau P-dg est une étape clé dans cette nouvelle stratégie, d’autant qu’elle s’est accompagnée d’une réorganisation de la direction : les deux cofondateurs restent aux manettes mais vont se concentrer sur la technologie et la production. Alban Mallet, prédécesseur de Dominique Corvez, est ainsi devenu le directeur technique (CTO) tandis que Romain Duballet demeure le directeur produit (CPO) de l’entreprise. Dominique Corvez va pour sa part gérer la mise en œuvre du déploiement.
Ingénieur-architecte de formation, ce dernier possède le savoir-faire pour organiser et déployer un nouveau business à l’international. Dans ses précédentes postes, il a notamment développé pour le compte de Lafarge un nouveau produit innovant, le béton fibré à ultra-hautes performances (BFUP), et dirigé son déploiement en Amérique du Nord à partir de 2013. Il a renouvelé cette expérience de développeur chez Eiffage à partir de 2019, pour le lancement d’une filiale dédiée à la réparation d’ouvrages d’arts et aux travaux spécialisés, puis au sein de la direction de la coentreprise EKFB au Royaume-Uni.
Autre étape clé : le nouveau projet de levée de fonds en cours, de plus grande envergure que les précédents, et qui cible cette fois-ci non plus des partenaires industriels mais des investisseurs financiers. « Après deux premières levées de fonds, l’entrée au capital de Vinci Construction, Shibumi International et Holcim France, la levée de fonds en cours permettra l’accélération sans précédent du développement de notre réseau mondial d’unités d’impression 3D connectées, capables de produire efficacement et localement des éléments de construction structurels sur mesure, sur base de la technologie XtreeE » résume Dominique Corvez. Il reste néanmoins discret sur l’objectif de montant recherché. Des discussions sont notamment en cours avec un acteur majeur du capital investissement.
Christine Gilguy